2013.10.15
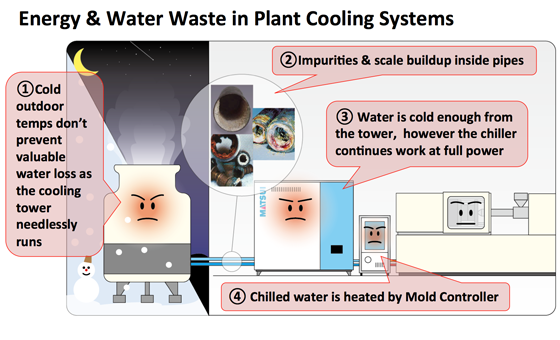
Toward “Doubling Wealth, Halving Resource Use” in molding factories (2) --- Is the waste of resource in molding factories is so huge?
2. How hugely we waste resources in molding factories
In my previous article I wrote the background of the Green Molding and what the Green Molding and factor4 mean. I also explained that the Green Molding and factor 4 (4 times resource efficiency) does not only help address the global poverty problem or the global environmental problem but also help to transform the molding factories into more efficient and profitable places and can be a key to survive and thrive in this global competition.
But if factor4 is feasible, that means the current resource efficiency of most molding factories is below 25%. Do they have such poor efficiency? Yes, unfortunately that is true. In this article I would like to show you how much we waste resources such as energy, resin, water and also time.
For example, let’s have a look at the water cooling process. The normal cooling tower unnecessarily evaporates dozens of tons of water every day. I must say 95% of the evaporation is unnecessary. It is not only a waste of water but it is the main cause of many troubles such as scale in the pipings and the molds, because the evaporation makes the concentration of the impurities higher and higher.
Many of your factories use chillers. In most cases they are always at full-capacity operation no matter how much the heat load is or even if the water from the cooling tower is already cool enough without Chillers . And in many cases, while a large quantity of energy is consumed to cool the water like this, water may be heated again using additional electricity by the mold temperature controler. These things seem so ridiculous but they happen all the time everywhere.
The waste of energy can be found also around the injection machines and driers. Naturally everybody knows it is very hot inside the molding factory. But all that heat itself shows how much energy we waste. And such waste of energy is doubled or tripled when you use air-conditioner to cool the room temperature down.
As you can see in the illustration the waste of resin happens in all the process. In addition to the runners or defective products, leftover resin almost always thrown away each time the job is changed, which will be huge when you frequently change the material or the color.
This shows the painting process which is sometimes necessary just to hide the poor quality of the surface of the molded parts. The painting process is a very energy-consuming process and also tends to have a low yield rate. As a result this process piles up the waste of resources once again.
As the waste of resource is so high, we believe we can achieve 4-times resource efficiency.
In my next article, I would like to introduce the Association of Green Molding Solutions which was formed to realize Green Molding & factor4 in molding factories.
- Getting Rid of Wasted Energy
- Getting Rid of Material Waste
- Green Molding in General