2013.09.27
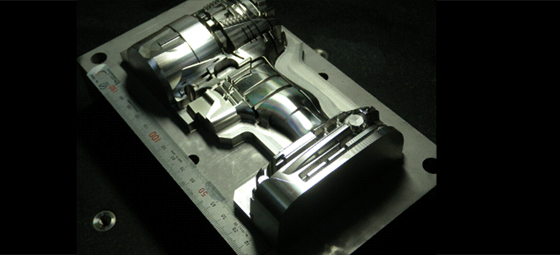
“Dramatic Advancement of Milling-Combined Metal Laser Sintering Technology and its Operational Enhancement”(1)
1. Introduction
OPM Laboratory Co., Ltd, officially licensed by Panasonic Corporation, has been constantly developing control software for milling-combined metal laser sintering technology ranging from fundamental algorithms to solution systems for ten years since the company’s establishment, and we have been in pursuit of enhanced development of crafting mechanisms at the same time.
We provide exclusive and indispensable laser and CAM systems for “LUMEX”, a metal laser sintering hybrid milling machine made by Matsuura Machinery Corporation.
We also have another face: we are power users who hold the world’s largest number of the said machines for mass production purposes. For your information, as for metal laser sintering hybrid machine production and its market entry, we have been granted development rights by Panasonic Corporation. From the perspective of enhancing Japan’s manufacturing capabilities, it is, in our view, favorable that there are multiple machine makers out there competing with each other, making their machines better and better, and through all this, making those machines more familiar and more widespread.
Before getting down to our subject theme, I would like to confess my memory of being unable to get to sleep. Being optimistic, I started this business 10 years ago, when this method was far from mature in mechanical and technological terms, leaving so much to be desired. Every day was a day of failure and difficulty. I’d often wonder if it would be really possible to put this into practice. Our company had long been on the verge of going bankrupt. Now that the market is so hot that you can’t see spend a day without seeing the term “3D Printer” in a lot of mass media such as newspapers and TV. In response, our company has been receiving four or five times as many inquiries as the average year. We are witnessing a major change taking place.
Here I would like to plainly review the laser metal sintering technology from the viewpoint of a user who I once was. I have been through a lot of difficulties as a user. I would like to contribute this paper for the sake of those who are considering incorporating this method into their molding technology. My utmost gratitude goes to those who have given us support over the years.
2. The reason why it is necessary to choose milling-combined method in order to apply metal laser sintering for high precision parts.
I assume a lot of people are familiar with the fact that metal laser sintering refers to a technology of piling up layers of metal powder melted by laser beam. The average diameter of the powder is 20~30μ. Basic explanation of the method is to be omitted here. The actual process is that 1400~1500℃ laser is fired at metal powder along the scanned line to melt and then solidify it. This principle is the same as laser welding, leaving residual stress inside molded objects. At the same time, stress is generated on the surface between the plate and the object, leading to warpage in the plate. Wrong designs will cause a crack in both the object and the plate, attain no precision and no practical value, leaving junk iron behind.
In order to apply this method for high precision parts, it is of great importance whether it is possible to relieve this stress, predict the extent of warpage and take appropriate measures.
As a matter of fact, this issue was recognized as an extremely important subject by industry-government-academia research panels of Strategic Foundational Technology Improvement Support Operation. Evaluation trials were carried out and a part of the results is shown in Graph 1. As this graph shows, it is clear that warpage doesn’t increase when the height reaches a certain point in regard to the plate thickness depending on object materials, object surface areas, plate thickness/plate material quality. Our company makes it a rule to set up the secondary process milling surface above the certain height of the object, after configuring proper plate material and thickness that meet the expectations of each requirements, by making use of forecasting curves of the extent of warpage that is caused according to the object volume and projected areas. This is mandatory if you are to produce a high precision product whose margin of error is within ±1/100 (one hundredth)
As for non-milling-combined metal laser sintering technologies, the base plate is only a plate and nothing more or nothing less, for the system has not function of measuring the parallel degree and position after the base plate is set up on the machine. What’s worse, it is also impossible to locate the center of the object from the end plane or from the drilled hole, as the plate itself is not positioned precisely and accurately. In addition, even though the galvano system is automatically corrected, it is not always assured that the CAD data is as reliable as it is stated in its specification due to the fact that there has been a long-time, repeated cycle of thermal expansion and contraction. Warpage problems are again a factor here. The plate gets warped the moment it is removed from the work table. As a result, there is no measuring the referential milling surface from the end plane and from the drilled hole. Metal laser sintering methods users pay their most attention to this. Nevertheless, the machine makers don’t pay as much attention to it, making virtually no effort to take proper steps for better developmental and research purposes. Our company views this matter as the most difficult when it comes down to mass production. We have been paying undivided attention to this matter as one of our top priority research and developmental assignments.
For these reasons and from a user’s perspective, we can definitely say that it is extremely hard to attain ±1/100 precision by means of metal laser sintering methods even if the object melted and solidified by laser goes through the secondary machining process. We have visited a lot of foreign users and exchanged views and opinions with them. And so, it is now evident that they have introduced this method not for the purpose of creating high precision parts but for the purpose of making medical products such as dental implants and artificial bones, or products in the field of design; the fields where high precision is not necessarily required. However, cylinder-shaped, rectangular cylinder-shaped, circular cone-shaped, pyramid-shaped objects and/or their complex rather simple shapes which can be processed by ordinary machines are partly created by this means.
Ten and several years ago in Japan, there was once a boom of introducing metal laser sintering, and there were several companies that actually did it. Hence, Japanese companies are highly aware of the warpage problems. As a result, there are few, in any, companies that are considering using metal laser sintering machines for the production of high precision parts. On the other hand, it appears that the companies in, say, China, Taiwan and Southeast Asia have little background information of the said technology. Many of those companies haven’t recognized this problem yet, which we view is quite dangerous.
What lies in the background of this situation is that similar sales promotion has been done by Western-based machine makers. By similar sales promotion do we mean that they promote 3D printer oriented manufacturing methods, which is expanding for personal use, even in the field of metal laser sintering. Resin 3D printing technology can be used to make a prototype for geometry confirmation purposes, but it is not plausible to apply this for mass production, which requires high precision.
We would like to put emphasis on;
A) the fact that consideration is not sufficient about the sequence between metal laser sintering machines and previous/after processes, in terms of processed standards and measurement standards.
B) the machine lacks necessary features; measurement and data feedback.
These two points are overlooked. Therefore, it is vital to stand on this viewpoint and make improvements.
We here would like to strongly advise those who read this paper to be very careful not to overlook these essential facts. If a user should introduce this method to make high precision die parts without any knowledge of this, applicability and operation rates will be minimized and eventually, the machine will end up in sitting idle in dust. Japan’s metal laser sintering hybrid milling technology has been developed and promoted through industry-government-academia cooperation to address the above-mentioned issues. We developed fundamental methods based on Panasonic Corporation’s basic patents and through Strategic Foundational Technology Improvement Support Operation schemes in the field of die and mold from 2003 through 2005. We think that we succeeded in developing market competitive methods, especially through Regional Revitalization Consortium schemes from 2006 through 2007. The team at the time was comprised of frontline companies and knowledgable university labs such as Panasonic Corporation, OPM Laboratory Co., Ltd, Kyushu Institute of Technology, Kanazawa University, Miyamaru Precision Mold Co., Ltd and Yamanaka Eng Co., Ltd, and we spent about five years to iron out the problems.
By employing this hybrid method, the machine is equipped with NC/machining spindles, but this doesn’t necessarily mean that the object is always milled. What should be noted here is that users are offered two options, and hence it is possible for them to select the best way in accordance with their demands and purposes. Let’s have a look at these points;
A) the method of creating only die reference plane to add secondary process to the object (Photo 2) in a case where the shape of the object is simple, making it more effective to finish it through secondary process than to mill it inside the machine.
B) the method of milling all the surfaces of the object (Photo 3) effective for shapes that have a lot of ribs and need a lot of electrodes.
Our company also makes the best selection in producing molds.
- Lowering Cycle Times
- Higher Dimensional Precision