2013.10.15
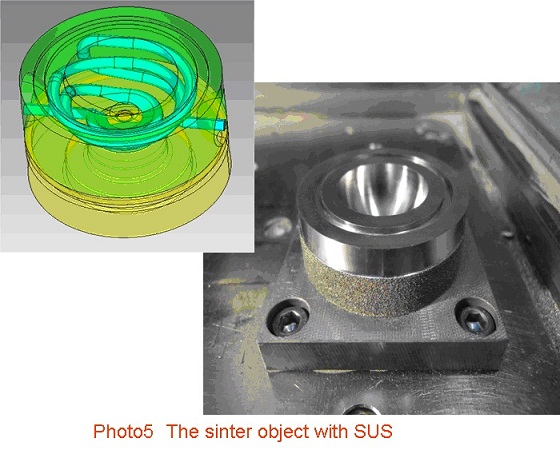
“Dramatic Advancement of Milling-Combined Metal Laser Sintering Technology and its Operational Enhancement” (2)
3. Standards for Adaptation and Machine Operation Techniques for High Precision Parts Production by Metal Laser Sintering
3.1 The Need for Measurement Standards
Take a look at Photo 4 and you can see the workspace of metal laser sintering hybrid milling machine LUMEX-Avance25 (Made by Matsuura Machinery Corporation). In order to produce high precision molds and parts, as is mentioned above, it is necessary to simultaneously measure and process die reference plane inside the machine. The photo shows how the special tooling is equipped in the work area of LUMEX, parallel degree is measured by dial gauge, positioning is being conducted by probe head. NC/machining spindles make it possible to correct errors by referring to actual data CAD/CAM numerical data, and give feedback before, during and after each process. This is a point which shouldn’t be missed.
3.2 Guidelines for Application of Molding
Although our moldable size capacity is limited within the framework of 250×250×185mm, a lot of users, it seems, have started to make potential business inquiries to us after they have done careful examination of their order. This is highly likely due to the fact that our industry has gained recognition and attention, and we are deeply grateful for this favorable trend. The horizontal axis of Graph 2 shows the volume of the objects we produced from April through July of 2013. Since the laser system of LUMEX was equipped with a 400W Yb fiber laser, shaping speed doubled compared with 500W CO2 laser, which has increased the business applicable volume of 600,000mm³ up to 1,000,000mm³. Of course, it is possible to size it up, but we do not recommend it for profitability and/or technical reasons as long as there is an extremely rare reason.
Graph 3 shows the estimated time of laser projection on the assumption that it is done by CO2 laser. It is now possible to secure stability in the time span ranging from 100 to 200 hours in terms of CO2 laser.
4. Hardness Level Increase of Metal Powder Materials and Applicability Expansion due to Mirror Surface Improvement
The material’s hardness had been viewed as the biggest disadvantage until several years ago, but our company has been putting our efforts into its solution. At this point of time, we have attained over HRC50 hardness through the Rockwell hardness testing method. This enabled us to produce molds with materials having better mirror surface, better corrosion-resistance and better rust prevention capabilities. These two kinds of materials we are going to mention just below are mainly used for mass production purposes.
① Purposes and characteristics of ultra high strength maraging steel (Photo 5)
Material type code: OPM-Ultra
Hardness: After sintering HRC33 / After aging process HRC50±2
Age hardening is possible at a low temperature of 475℃, and plastic intensity is limited to an extremely low level of below 0.1%, with high ductility and with quite good strength-to-weight ratio.
② Purposes and characteristics of hard and corrosion-resistant SUS
Material type code: OPM-SUS
Hardness: Right after molding HRC52±2
Quenching and tempering are possible. Quite good mirror surface. Good corrosion resistance and rust prevention capabilities. Suitable for PPS, super engineering plastics and so on.
- Lowering Cycle Times
- Cancelling Problems with Gas
- Lightening Part Weights
- Higher Dimensional Precision