2015.02.17

Resolving Color Inconsistency by Blending System
Resolving Color Inconsistency by Blending System
There are hidden problems of [Waste] and [Risk] in a blending system. [Waste] refers to the waste of disposal material and the waste of time when injection molding machine stops production when changing the colors. [Risk] indicates the problem of color inconsistency.
Firstly we will address the issue on how to resolve the problem of color inconsistency. Figure 1 below illustrates the relation between color inconsistency and the waste occurred.
The reason for color inconsistency caused by blending system could result from the blending system, the properties of raw material or foreign disturbance.
Color Inconsistency Caused by Blending System
The reason to why color inconsistency happens can be classified into two categories which are [Measuring Accuracy] and [Mixing Accuracy].
In the case of [Measuring Accuracy], you can check the record of measured value when the gravimetric blender is used and find out the reason in the early stage. This can avoid the problem to be perpetuated
On the other hand, the color inconsistency caused by [Mixing Accuracy] is more difficult to be discovered and resolved. This is because firstly you have to quantify the phenomenon of color inconsistency. It is labor-intensive and a lot of time is needed. After you quantify the color variation, you have to introduce new mixing steps and check the variation again. Much manpower is required.
There are many methods of blending. For Matsui, the mixing method used after measurement is known as [Critical Rotating Mixing] which could increase the [Mixing Accuracy].
For mixing evenly, the material has to be mixed by stirring back and forth. During this process the mixing is affected the gravity force. The Critical Rotating Mixing is designed by taking this gravity force into consideration. Most of the mixer in Matsui blending system have been standardized.
In case the problem of mixing accuracy happens because of the material properties, it is effective to use the synchronized mixing system introduced at below.
Color Inconsistency caused by the properties of mixture
For the color inconsistency caused by mixture’s properties, there are two reasons. One of them is the difference in material size and the other is the difference in material density. In case the difference exceeds a certain limit, the material could not be mixed well by stirring. As the mixing of the material happens longer, the denser material will be separated to the bottom creating a two-layer phenomenon.
For example, in case of mixing the [virgin pellet and talc-included master batch], the talc-included pellet will sink to the bottom since its density is higher.
Another example of pellet size will be the mixing of [fiber shape additive and virgin pellet]. The shape of fiber could be long and thin or thick and big. In both shape cases, their sizes are bigger than a normal pellet.
Upon mixing them, the smaller pellet will pass through the gap between bigger pellets and this results the bigger pellet to be raised to the upper layer.
In this case, synchronized blending method is being used. This is a method without using the process of stirring. To explain about the synchronized blending, normally the image of [Kintaro Candy] is being used. Kintaro candy is in bar-shape. When you cut it in slice, each of the cross-section shows the same Kintaro face.
Here we would like to explain that it is always the same mixing ratio when consuming the slice.
This phenomenon is shown at Fig 2. Then how do we get this state from a blending system? The method is using synchronized blending method. It is shown at Fig 3.
Here we introduce the blending systems. For synchronized blending, there are volumetric synchronized blending system in Fig 4 and gravimetric synchronized blending system in Fig 5.
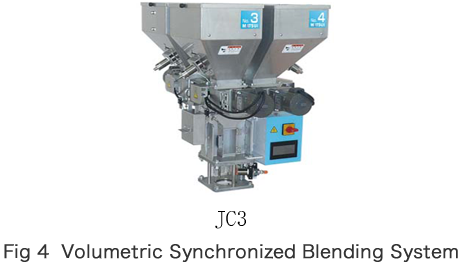
Color Inconsistency Caused by Foreign Disturbance
The main reason of color inconsistency caused by foreign disturbance is from static. Static occurs when the air is dry. Therefore, the problem of color inconsistency often happens during winter.
In order to remove the static and result uniform material flow, ionizer has to be installed inside the hopper.
Figure 6 illustrates the color inconsistency due to static and the schematic after improvements are implemented. Meanwhile Figure 7 shows the diffuser and Figure 8 depicts the ionizer.
To be continued.
- Getting Rid of Wasted Energy
- Getting Rid of Material Waste
- Improvement of Surface Quality & Value
- Resolving Color Variation