2014.10.09
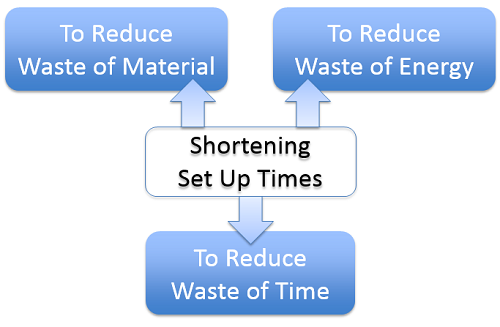
Shortening Set-Up Times during Material Changes
Shortening Setup Times during Material Changes
What are the advantages of shorter setup times?
The operating time of an injection molding machine is roughly 4,000 hours a year. If we can reduce the down time of this machine by reducing the length of setups, we can increase production time, which leads to more output.
In addition to this, we can lessen the energy consumed to produce each product. This is because every machine consumes energy even during down time. In fact almost as much energy can be consumed while the machine is down as while running production.
And shortening setup time can usually reduce material waste, as I discuss later in this article.
So shortening setup times can increase the output and reduce costs by reducing “time”, “energy” and “material” consumed for production.
There are two kinds of set up processes, one is “on line set up” and the other is “off line set up”.
“On line set up” is done with production stopped. “Off line set up” is done while continuing production. To maximize output, it is necessary to minimize “on line set up”. “Off line set up” is useful to reduce “on line set up time.
Let’s consider how we can reduce down time when materials are changed.
Let’s take a very simple example of an injection molding line with one dryer beside the machine (see figure below). In this case there are mainly four tasks to complete in order to change materials. Each task requires time, as shown in the figure below.
As for the time required to dry the new resin, we can easily eliminate delays by using an extra dryer to “pre-dry”. Other tasks will require around 40 minutes.
If the yearly operating time of the injection machine is 4000 hours, and we change resins once every eight hours on average, we then change resins 500 times a year.
This means if we could reduce the set up times for these changes by 30 minutes, we could save 30 minutes * 500 times = 15,000 minutes = 250 hours, and use that time to increase output.
If you presently have 16 injection molding machines, this time savings in could increase production output to equal that of 17 molding machines!
The next figure shows an example of the line with much less down time.
The production line shown above has 3 major advantages.
1) The amount of material in the hopper on the machine is minimized.
2) The amount of resin conveyed to the injection machine each time is minimized.
3) The remaining of the resin in the hose can be eliminated.
To realize these advantages we use the combination of “Push damper” below the dryer and “APHG”, hopper with a minimum charge capacity, on the injection machine.
1. “Push Damper”
The“Push Damper”is a dosing valve with a vacuum take-off port mounted below. It can restrict the amount of resin conveyed to around 50 to 150 grams. It functions as in the figures below.
2. APHG; A vacuum receiver that stores a small amount of material
The APHG is mounted on the injection machine as a vacuum receiving hopper. It is used to store only a small amount of resin such as 60 to 100 grams. By combining the “Push Damper” and APHG, the amount of material conveyed and stored on the molder can be minimized. This leads to a greater advantage in shortening setup times and reducing material waste.
With the Push Damper + APHG System you can eliminate resin left in feed hoses and the time normally used to clean it out. And if you stop resin conveying just before you stop production, you can also eliminate time normally spent getting rid of resin remaining in the hopper. This also minimizes the time needed to purge resin remaining in the cylinder.
The following table shows the expected merit gained by applying the solutions above.
Merits of shortening set up times during resin changes
To be continued.
- Getting Rid of Wasted Energy
- Getting Rid of Material Waste
- Shortening Set Up Times