2014.05.20
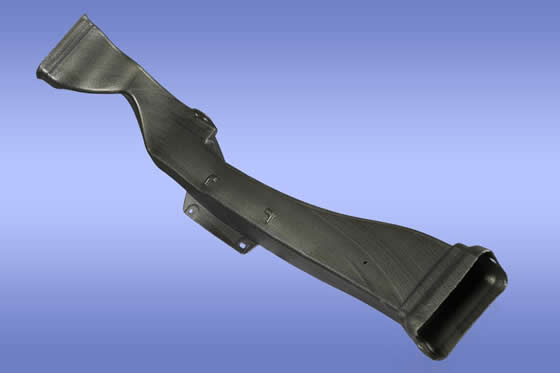
Newly developed MuCell® blow molding process for automotive plastic parts offers significant weight savings
Newly developed MuCell® blow molding process for automotive plastic parts offers significant weight savings
As a leader in providing lightweighting solutions to the plastics injection molding industry, Trexel, Inc. has extended its MuCell processing solution to blow molded automotive components. In working closely with their OEM and Tier I customers, the company has recognized the need for lightweighting plastic parts beyond the traditional and proven injection molded interior, exterior and under the hood applications.
To develop this robust MuCell blow molding process Trexel worked with ABC Group in Toronto Canada, one of the leading providers of blow molded products to the North American automotive industry. Over the last year, engineers from Trexel and ABC Group have been diligently working together on the development of MuCell blow molding. As a result of these efforts the first Mucell blow molding process was achieved with an automotive application. The part is a reinforced Polyethylene air duct with 1.5 – 2mm wall thickness. As a result of the Mucell process the density reduction is 41% of the foamed material, resulting in a 32% net weight saving of the finished part compared to solid.
“We are very excited about the results we have achieved so far,“ said Steve Braig, President and CEO of Trexel, Inc. “Commercial development of additional MuCell foamed blow molded parts including design and material optimization should result in higher than 40% weight reduction compared to the solid molded part. These results will be very attractive to OEM and Tier suppliers, and ultimately to car buyers who will enjoy improved fuel efficiency of their vehicles.”
Besides weight savings, there are several highly desirable attributes of foamed versus solid blow molded parts: the microcellular material structure improves thermal insulation and also provides for improved acoustical properties. The MuCell technology, a physical foaming process, also has several advantages over the use of chemical foaming agents: no chemical reaction at narrow processing window, no chemical additive residue in final parts, and most importantly, MuCell foamed parts can be recycled in their original polymer designation; the process does not alter the chemistry of the polymer.
About Trexel
MuCell® Microcellular foaming technology was originally conceptualized and invented at the Massachusetts Institute of Technology (MIT) and in 1995 Trexel was granted an exclusive worldwide license for the further development and commercialization of the technology. Today, Trexel is the exclusive provider of the MuCell® microcellular foam technology and maintains an extensive global patent portfolio. Trexel provides world-class engineering support, training and other design and processing services, as well as the equipment and components integral to the MuCell® process.
From the global headquarters in Boston, Massachusetts, Trexel operates a state of the art plastics processing development laboratory, supporting plastics processors with the definition and implementation of leading and differentiating plastic molding technologies.
In support of a global client base, Trexel operates subsidiaries in Europe, Japan and Southeast Asia with competent plastics processing engineering capabilities. Trexel’s worldwide subsidiaries are augmented by a network of competent independent representatives and distributors.
- Getting Rid of Material Waste
- Lowering Cycle Times
- Lightening Part Weights
- Higher Dimensional Precision