2014.05.20
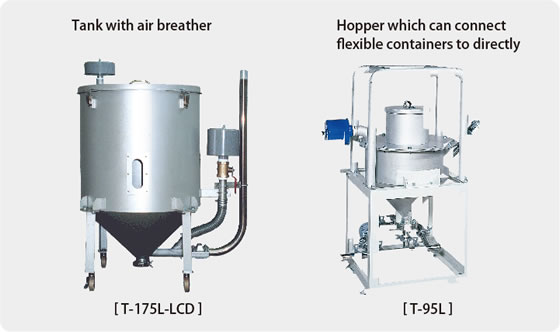
Achieving Green Molding (9)
Continued from my previous article.
Matsui proposes “factor4” as the primary target in molding factories. As a partner for resource conservation, our goal is to help customers achieve 4-times resource productivity by eliminating waste and increasing output.
In the previous issue (sequel to the “Cancelling Problems with Gas”), we talked about a dry ice blasting system for safely and effectively cleaning gaseous residues off the mold surface. (by Showa Denko Gas Products Co., Ltd.)
Today, I will talk about solutions for Eliminating Contamination during the production of a molded plastic part.
‘Contamination’ which has been called ‘Contami’ for short, refers to unwanted foreign substances entering the product or packaging during the manufacturing process.
Contamination’ is but a single word, yet there are a variety of opportunities, and types of contaminants that can cause trouble in the production of molded plastic products. From the production of raw material, to storage and transportation to the molding facility, safeguards must be taken to prevent exposure to foreign matter. Even after successful delivery to the molding plant, raw material must be transferred inside to drying, blending and other handling systems prior to reaching the molding machine. These transfers and contacts with different systems provide more opportunity for suspended solids, oil mist, chemicals etc. to contact the raw material. There may even be metal powder present caused by frictional wear inside the metal feed pipe. Other hazards include residue from purging compounds used to clean the injection barrel, or gaseous substances lingering within the molding machine.
Depending on the product type, there may be higher purity standards and therefore stricter manufacturing requirements. For example, optical parts, sensors, electronic and medical components are very sensitive to even low levels of foreign matter. Also, Clear parts and small precision molded products are adversely affected by the slightest presence of contamination. Troubles include clogging at the nozzle or short shots in the mold. Variations can occur in part strength, color and texture. For example there is the risk of electrical shorting if a precision connector is manufactured with contamination in the metal contact point. Transparent products, especially lenses are rejected immediately if impurities are discovered.
o solve these problems, contamination risks must be addressed all through the manufacturing process to the delivery point. Necessary precautions should be taken wherever contamination risks are present. It is assumed that the level of precautions will be in balance with the type of product and the quality level required. For example, it may be necessary to manage contamination risks for the entire plant, or possibly just installing a clean “room” for a particular set of products. Inside the clean room special equipment is used and environmental handling systems manage particulate counts in the air to a specific standard.
Matsui offers a variety of systems and equipment designed for clean room environments. Let me now introduce some of these products.
To feed resin from bulk storage to the plant…
▼Material storage tank for clean room production
This material tank is designed and built for contaminant prevention.
The tank’s corrosion resistant structure is made for easy cleaning.
The special filtration system captures particles from 10μm ~ 0.1μm,
preventing foreign materials from entering.
▼HEPA Filter / Suction Nozzle w/ Filter
This type of equipment is essential for automatic operation of the clean room molding line. In the material conveying process, dust is prevented from escaping into the open air. Likewise, dust other small contaminants are prevented from gaining access inside the tank.
▼Magic Catch
This device protects against tramp metal contamination with a magnet. Scraps of iron such as bolts, washers and nails etc will be captured before causing catastrophic damage to processing equipment. By simply installing Magic Catch in the material feed hose, the molder’s critical screw, cylinder and mold will be better protected.
▼Abrasion Resistant Plumbing(Kanuc Processing)
This is a hardening technology different from the usual coatings used to protect metallic surfaces. Hardening is possible because film flaking and dimensional changes are minute.
Supplying the molder with dried resin…
▼Drying & Conveying System for Optical Products
Exclusive Optical System, incorporating Matsui’s knowledge and experience for contaminant prevention in one compact platform.
▼Thermal Conduction Vacuum Dryer
In a vacuum environment, drying material is made easier and less heat is required. Also a vacuum drying system doesn’t require outside air to be heated and pushed through the hopper dryer, so the risk of contamination is minimized. Also less heat is and very little oxygen is present, so material oxidation and discoloration are eliminated.
▼Thermal Conducting Dryer
The thermal conduction dryer uses a low air flow volume to reduce contamination risks. Also, a nitrogen gas purge can be used, preventing oxidation and yellowing of the material.
▼Aero Power Hopper
This vacuum loading receiver removes dust and mixes material at the molder’s feed throat. These benefits are achieved by controlling and using the conveying airflow during material feeding.
For material recycling…
▼Non-Contamination Granulator
Matsui’s granulator is designed to prevent cross-contamination. It is also available for recycling of transparent resins.
▼Metal Detector
Removes metallic contaminants in the resin stream with a special sensor.
Can sense and remove metallic particles that are not detected by magnetic separator.
In addition we provide the right equipment for all molding lines.
Please also refer to our web site ‘factor4 solutions / 6. Eliminating Contamination’.
⇒ http://matsui-mfg.net/factor4_solutions/6/
Article titled “Towards the realization of green molding” will now terminate.
Thank you for your time.
- Eliminating Contamination