2014.03.13
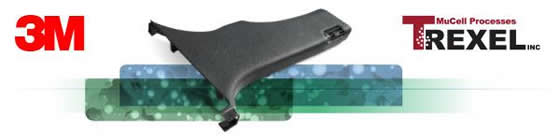
Combined Trexel Technologies and 3M Revolutionize Lightweighting of Plastics; 20% Density Reduction Proven with Molded Auto Parts
Combined Trexel Technologies and 3M Revolutionize Lightweighting of Plastics; 20% Density Reduction Proven with Molded Auto Parts
To address demanding lightweighting needs in the plastics industry, 3M and Trexel have demonstrated a breakthrough that enables manufacturers to realize 20 percent density reduction of finished plastic parts with mechanical properties comparable to standard formulations. Manufacturers can also reap improvements in dimensional stability, process throughput and sustainability. The achievement signifies one of the world’s largest advancement in the lightweighting of plastics. The breakthrough is especially significant for the transportation industry and namely, automakers, as reducing overall vehicle weight is a key initiative as they face increasingly stringent fuel economy standards, and carbon emission reduction targets.
3M, a manufacturer of high-strength glass bubbles, and Trexel Inc., the exclusive provider of MuCell® Microcellular Foam injection molding technology demonstrated the revolutionary results by combining a variety of optimized polymer resin systems using 3M Glass Bubbles iM16K with Trexel’s unique MuCell foaming technology.
“This marketing collaboration between Trexel and 3M is a game changer for the plastics industry – especially in the automotive sector,” said Steve Braig, president and chief executive officer at Trexel. “It’s challenging to take weight out of plastic parts without sacrificing strength, durability or function. Through this innovative approach, customers can speed up the process and significantly reduce weight, while maintaining the part integrity.”
According to Trexel and 3M the new process can be replicated at any facility around the world for plastic parts, such as automotive under the hood, interior and exterior and other molded parts. Braig went on to explain that significant weight savings can be achieved in a variety of resin systems including both filled nylon and filled polypropylene, especially significant to automakers as even a small weight reduction can make a difference as incremental design and parts adjustments can add up quickly. As a result, automakers consider every aspect of a vehicle – from the smallest bracket to the engine that powers it for potential weight savings.
“Used alone, 3M Glass Bubbles or Trexel’s MuCell foaming technology can realize from eight to 10 percent reduction in weight while maintaining mechanical and physical properties,” said Doug Rowen, global business director for 3M Glass Bubbles. “But combined, the technologies complement each other resulting in significantly increased weight reduction, cycle time reductions and improved dimensional stability of finished parts.”
The combined 3M and Trexel technology also offers several additional benefits including lower cavity pressure resulting in reduced clamping tonnage, no sink marks, and increased sustainability resulting from the use of less petrochemical feedstock.
As part of 3M’s line of high-strength glass bubbles, the company’s latest product in the family, iM16k, is especially relevant for automotive applications. iM16k is a high-strength injection molding grade glass bubble for polypropylene, polyamide and other polymer systems and features crush strength of >16,000 psi making it uniquely suited to survive injection molding and compounding processes. Incorporating glass bubbles, like iM16k, into the process improves dimensional stability, resulting in less shrinkage and warpage – thereby reducing reject parts and reprocessing. Manufacturers can also increase process throughput when using resin systems filled with iM16K as there is less finished part mass to cool, reducing cycle times by 15 to 25 percent.
Alternatively, MuCell foaming technology uses the controlled use of gas to create a foamed part, resulting in high quality precision and engineered plastic components, while greatly reducing production costs associated with lower material consumption, shorter molding cycle times, and reduced machine clamping tonnage requirements. The MuCell process enables automotive component manufacturers to lightweight plastic parts for overall vehicle weight reduction and improved fuel economy. The process also leads to predictable and repeatable part geometry, allowing for the use of lower cost polyolefin resins without warpage or distortion.
“The combined technologies result in unprecedented mass reduction in injection molded parts,” adds Braig. “Adding 3M Glass Bubbles iM16K and Trexel MuCell processes to the design freedom of plastic parts results in reduced material density which will lead to a new dimension of weight savings in plastics. Both 3M Technical Service and Trexel processing engineers globally are ready to assist customers with their demanding lightweighting objectives” Braig said.
“While both 3M and Trexel technologies have proven unique benefits that help the industry achieve weight reduction objectives in many applications, the combined technologies have demonstrated even better weight reduction performance, without sacrificing critical performance requirements.” said Rowen.
For more information regarding 3M Glass Bubbles, visit
http://www.3m.com/engineeredadditives
For more information about the Trexel process, visit http://www.trexel.com
About Trexel
MuCell® Microcellular foaming technology was originally conceptualized and invented at the Massachusetts Institute of Technology (MIT) and in 1995 Trexel was granted an exclusive worldwide license for the further development and commercialization of the technology. Today, Trexel is the exclusive provider of the MuCell® microcellular foam technology and maintains an extensive global patent portfolio. Trexel provides world-class engineering support, training and other design and processing services, as well as the equipment and components integral to the MuCell® process.
From the global headquarters in Boston, Massachusetts, Trexel operates a state of the art plastics processing development laboratory, supporting plastics processors with the definition and implementation of leading and differentiating plastic molding technologies.
In support of a global client base, Trexel operates subsidiaries in Europe, Japan and Southeast Asia with competent plastics processing engineering capabilities. Trexel’s worldwide subsidiaries are augmented by a network of competent independent representatives and distributors.
- Getting Rid of Material Waste
- Lowering Cycle Times
- Lightening Part Weights
- Higher Dimensional Precision