2014.02.17
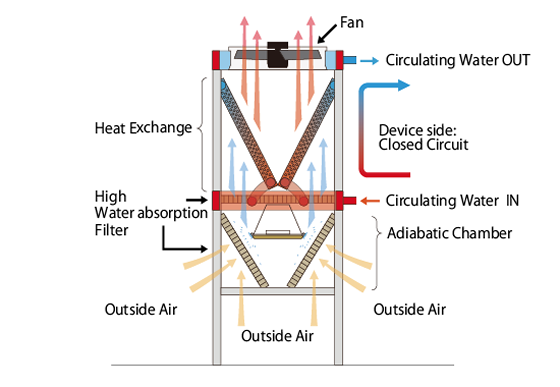
Achieve Green Molding (6)
Continued from my previous article.
◆ Solutions for Solving Water Quality Issues (2)
Matsui proposes “factor4” as the primary target in molding factories. As a partner for resource conservation, our goal is to help customers achieve 4-times resource productivity by eliminating waste and increasing output.
In the previous issue (“Solutions for Solving Water Quality Issues”), I explained how a conventional open loop type cooling tower can eventually cause problems throughout the manufacturing plant and mechanism of piping congestion. These troubles can be traced to the “open” style cooling method shared by all these towers.
In an open type cooling tower, water comes in direct contact with the outside air. The evaporation that occurs causes some water to be lost, while effectively cooling the water that remains. Unfortunately minerals & sediments are continuously left behind by the evaporated water. Over time, the open tower creates rising levels of these unwanted materials in the entire cooling system.
The closed-loop cooling tower was designed specifically to lower water loss, reduce water contamination, and to improve water quality. While generally better than the open tower, closed cooling towers are not without their own issues.
The illustrations below show how these 2-types of cooling towers function.
As you can see, the closed type cooling tower does not cause rising mineral & sediment levels in plant cooling systems. This is prevented by eliminating contact between the plant process water and outside air. Also a closed tower will eliminate some of the constant water makeup necessary in an open system from evaporation. Therefore, the use of a closed tower will reduce or eliminate many common problems and costs of the conventional open system. You can say the closed cooling tower a very good choice for better productivity and lower operating costs.
While closed type cooling resolves many common problems with plant water, there are other serious problems to address.
Both systems are similar in the mechanism of cooling used. For example in both systems, water is in contact with outside air. Therefore, dust in the air, plant spores, microorganisms and various suspended solids can enter the cooling water supply. The results are that algae, fungi, bacteria and legionella bacteria can grow and spread. Many factories inject a treatment agent to prevent mass generation of these biological agents as well as for rust and corrosion.
In fact, both types of cooling tower lose water to evaporation, and disperse mist to the outside air which may contain harmful ingredients.
How much water (and harmful mist) can be dispersed?
There is a way to calculate and identify the quantities.
For example, a small open type cooling tower with 100RT, would have water circulation of approximately 78 tons / hour.
The scattering rate of cooling water is about 0.1% of the circulating water.
So for one-day the amount scattered is…
78,000 (L) × 0.001 (0.1%) × 24 (h) = 1,872 (L)
Just one 100RT tower can scatter almost 2,000 liters every day.
In other words, people working in the vicinity these types of cooling towers, are constantly exposed to a biohazard and chemical-hazard.
In some regions like Japan where water quality is high, these problems are not common. But in the areas where water quality is low, or where people are working diligently to protect the environment, a solution was needed. The next generation cooling tower called a “dry cooler” was developed. The “dry cooler” has already been tested successfully in the harshest environments. (Italy Frigel investigation)
The Association of Green Molding Solutions is focused on helping our industry positively affect global environmental and poverty challenges, while increasing manufactures’ profits at the same time. As a member of AGMS, Matsui enthusiastically recommends the dry cooler known as ‘ecobrid’ of Italy’s Frigel.
In the ecobrid, concentrations of minerals / sediments and the scattering of the toxic substances are not created. Please see the illustration below.
High water quality in the factory cooling system will be maintained over a long period of time. The cooling water supply is not in contact with the outside air, as in a closed cooling tower. The major difference between the ecobrid and other types of cooling towers, is the cooling method. Both the ‘open type’ and ‘closed type’ tower transfer heat from the process with water. On the other hand the ecobrid, removes heat from the process by passing low temperature air to the heat exchanger. That’s why it is said to be ‘dry cooler’.
When the outside air temperature is low, the temperature of the circulating water goes down by simply passing through the heat exchanger. When the temperature of the circulating water cannot be cooled sufficiently by passing through the exchanger alone, a cooling fan is activated. Air is pulled by the fan across the outside of the heat exchanger increasing heat transfer. If still more cooling is needed, water is sprayed onto a superabsorbent filter placed at the air intake, further cooling the air volume.
Water used for spray cooling is only done only in trace amounts. There are no toxic substances because tap water is used. Therefore there is no need for water treatment chemicals. Also, because the sprayed water will quickly evaporate, bacteria and algae do not breed.
The advantage of ecobrid as compared to other dry-coolers is that the degradation of the device due to the water will not occur. By providing a unique mechanism (adiabatic chamber), the water does not directly contact the heat exchanger.
When compared to the ‘open’ or ‘closed’ style cooling tower, Ecobrid’s water-saving rate is approximately 95%, and power saving rate is approximately 25%. Algae, scale, bacteria etc. will not occur in the Ecobrid. There is little need for maintenance with Ecobrid. Return on Investment is estimated at 1~3 years. Traditional towers are designed for a seven year life. However ecobrid is designed for a 20-year life span, or almost 3-times as long.
The choice will become clear, the more closely these cooling systems are studied. ecobrid is the best, most economical and environmentally sound choice.
- Solving Water Quality Issues