2013.11.18
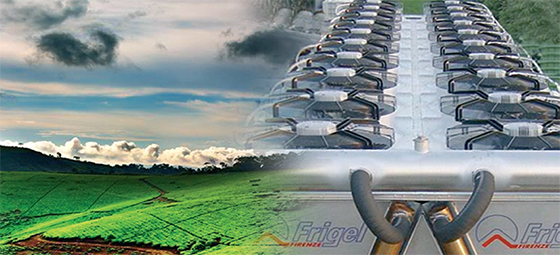
Process Control & Cooling and How it Affects Us All: (2)
Continued from my previous article
Facts about Fresh Water
• About 3% of the worlds water supply is fresh water
• Of this amount only 30% is easily accessible to humans
• Therefore 1% of the Earth’s water is available to us to use as drinking water
• Naturally we have to recycle fresh water by filtering and chemical treatment to supply our homes, businesses and factories
• Therefore, using water wisely and not polluting it with dirt and chemicals helps us today, as it helps the future generations with not only cost, but more importantly fresh water availability
Health, Safety and the Environment
Older less technologically advanced methods or cooling, such as wet evaporative cooling towers, are not only costly to operate and inefficient but they are also a potential health threat to the general public, employees, and our families.
A cooling tower is a cooling device used to cool industrial processes such as injection molding. It works by showering the warm process return water from the top of the tower through a series of nozzles and internal slats and louvers to allow air to be sucked through (or in some case blown) through the shower of water. The cooled water is then stored in a tank or sump to be re-circulated through the process whereby it gathers the process heat and is again pumped to the top of the tower for cooling.
When the air passes thru the water to cool it the air gathers up droplets of water in a mist. Often this mist is called tower drift. This mist is then blown out of the top of the tower and can travel for hundreds of meters before settling on the ground. The danger is that this tower drift when inhaled by humans can sometimes contain the Legionella bacteria which is a lethal form of pneumonia that is recorded as causing death in as many as 40% of the patients that contract the disease1
To prevent the propagation of the Legionella bacteria and the health risk, all users of cooling towers must have their towers professionally treated by specialist water treatment companies with biocides. However, this creates an additional health and environmental problem.
As we have reviewed a cooling tower cools the water by evaporation and in addition looses some water by drift, on average a cooling tower looses at 1.5% of the hourly flow rate of the cooling system.
If we consider an average injection molding business with 50 machines may have an hourly flow rate of 150 cubic meters per hour (m3/h) (each cubic meter is one thousand liters) then the system is loosing 1.5% of 150,000 liter per hour or 2,250 liters per hour of lost cooling water. This lost water is continually replaced from the factory or building water supply.
1 Source: Australian Channel 7 News June 2013
There are two problems created with this constant loss/addition of water:
1. The dissolved solids & airborne pollutants in the water system do not evaporate therefore continue to increase in concentration and thus posing a scaling and contamination risk to the equipment being cooled
2. The various chemical biocides and inhibitors also do not evaporate or disperse at the same rate as the water therefore these levels will continually vary and in some circumstances to a level which can also be health risk and damage equipment
Therefore, to resolve both these issues a cooling tower must be set up to blow water down the drain to exhaust the solids, pollution and out of balance chemicals. This water blow down obviously contains diluted amounts of harmful chemicals plus the high concentration of solids and pollutants, all of which must be filtered and purified before it is returned to the city water supply. This is typically not free and is a rapidly increasing cost like energy.
Applications Part 1 – Overview
In today’s modern work place we say we strive to be efficient, reduce energy, protect the environment and do all this with the economics that make it financially viable.
At Frigel we say we focus on:
• Safer worker conditions
• Less polluting of the environment
• Less wasted product that is made out of specification
• Less wasted time because production is too slow
• Less wasted energy because the process uses old technology
However, when we look at many of the common business indicators we seem to measure our success in many other ways:
1. Profit and loss
2. Cost reduction
3. Key Performance Indicators (KPI)
4. Coefficient of Performance (COP)
5. Return on Investment (ROI)
6. Return on Assets
Frigel can offer a bridge between, “what we say we need to do”, and “what we can demonstrate we can do” by offering high performance process control and cooling, that respects worker safety, the environment, and is the basis for improving control over the process thus improving productivity and profitability. All this plus an ROI that in is often less than 24 months!
All Frigel customers are offered a benefits analysis plus a return on investments analysis (ROI) and in most cases these ROI analysis identify a payback period between 1.5 to 3 years. What does this mean to an injection molding company? Lets take an example of a German manufacturer who in June 2013 invited Frigel to provide an analysis of proposed benefits.
Our team made a four hour audit of the customer’s 37 machine factory and then prepared a budget customer proposal. The proposal indicated that a USD$1.0 million investment would be rewarded by an estimated ROI of 2.0 years based on energy, water and maintenance savings plus a proposed 10% productivity gain. The customer was very interested as they were preparing to build a new factory and the Frigel Ecodry System for the new factory has much lower installation costs than a conventional central system.
Frigel provided the customer with a loan Microgel for a seven day trial on various machines and applications. In the first 24 hours the customer tested the Frigel Microgel on three machines and saved 7%, 10% and 14% cycle time respectively. This is in addition to reduced time on mold changes via the innovative Frigel Drain Kit option. Factories are not free to build, machines are not free to buy and great staff require training and development so it makes perfect sense to maximize the performance of your equipment.
The customer who had requested a proposal for their new factory has now also asked for a proposal for their existing factory to take advantage of these proposed savings.
In another example a Frigel customer recently purchased expensive German and Swiss injection molding systems to produce the cartridges for silicon filler for use in bathrooms and kitchens. During an introductory Frigel Corporate presentation the customer asked the Frigel Technical Sales Person to view this system and assist and evaluate a quality problem they had. The issue they had was a 6 to 10% random cracking failure rate during the mandatory drop test required by the global OEM customer.
The Frigel person quickly zeroed in on the variations of the chilled process water temperature as being a likely cause of the “random failure”. A Frigel Microgel was quickly made available for a seven day test period and because of the very tight tolerance on process water temperature control, the customers cracking quality problem was immediately resolved. The customer immediately bought the Microgel and has since purchased a complete Frigel Ecodry System for their factory.
Frigel delivers unparalleled process control and cooling and therefore is helping to build the bridge between:
Corporate profitability and corporate responsibility!
(to be continued.)
- Getting Rid of Wasted Energy
- Lowering Cycle Times
- Solving Water Quality Issues