2015.05.14
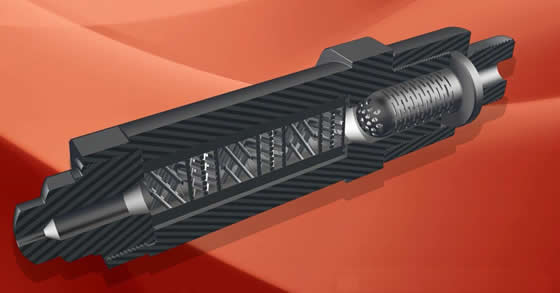
RUMASS Static Mixing Technology in Injection Molding Processes
RUMASS Static Mixing Technology in Injection Molding Processes
Briefing
As the price increase in all kinds of raw material and additives, together with higher labor costs all over the world, the top priority of plastic product manufacturers is improve productivity and lower production cost in order to be more competitive.
RUMASS Static mixing nozzle is an ideal solution which can be simply applied and gives a stable process performance. Through this technology, product appearance can be significantly improved with lower scrap rate, in many cases, it’s even possible to reduce dosage of additive and shorten cycle time.
Introduction
Static mixer is a high efficient mixing device without movement. The basic principle is to change melt flow direction by fitting mixing elements into nozzles, so to achieve good a distribution of additives and mixing with different melts qualities.
Since 1970s, static mixers have been used in chemical, food, textile and water treatment industries and got excellent results. RUMASS static mixer is an advanced element device, the difference between static mixer and dynamic mixer is: Static mixer has no moving parts, it uses the melt flow and internal elements structure to achieve mixing and form a unique melt structure. RUMASS static mixers is stands for more mixing effectiveness, lower energy consumption, smaller sized design, less investment and continuous production.
Rumass static Mixer for Injection molding Proces
Polymers to process with RUMASS static mixers
Thermal Plastics | LDPE, HDPE, LLDPE, PP, PS, HIPS, etc |
---|---|
Engineering Plastic | POM, PMMA, TPU, PET, PBT, SAN, ABS, LCP, PA, etc |
Composite | Glass Fiber (length<8mm), mineral filler |
Foaming Material | PS, PE, PP, PET, etc |
How is homogenized melt achieved?
Laminar mixing performance with RUMASS ZYM mixer is achieved through repeated separation, transformation, gentle elongation and rotate each mixing element by 90°. Therefore melt is spread into large number of small layers. RUMASS static mixer is assembled by several similar structured mixing elements. The more elements, the finer the layers; the finer the layers, the better the homogenization.
Homogeneity given by 8 mixing elements at flow ratio 1:1)
Remark: Above picture shows a mixing performance without screw plasticization.
Adding 4-6 mixing elements can dramatically improve color mixing.
Injection molding sample before and after mixer installation
Improvement due to better homogenization
1. | Pigments, and master batches can are be well distributed into the melt flow, the stable coloring, specially eliminate color streaks caused by master batch and low dosage of pigment and master batch. |
---|---|
2. | Eliminate color differences |
3. | Reduce coloring cost, even for light colored parts |
4. | Homogenize the melt, prevent bright spots |
Injection molding sample before and after mixer installation
Temperature Homogenization
Injection molding machines are installed with screw, which often creates an unsatisfied temperature distribution in the melt. This irregular temperature melt layers leads to temperature variations caused by screw performance. So after installation of a RUMASS static mixer inside the nozzle, a flat temperature profile can achieved as follows:
Temperature Profile Without a Static Mixer
Temperature Profile With a Static Mixer
Remark: In order to compare a relevant temperature distribution profile, tests were done on an extruded multilayer die cast PE film with screw L/D ratio of 34:1.
Improvements due to improved melt temperature distribution
1. | Eliminates flow lines, especially for ABS and engineering polymers, therefore better product appearance |
---|---|
2. | Improve flow and parting lines caused when “cold resin” meets “hot resin”, therefore better product appearance |
3. | Consistent part dimensions, therefore less distortion. |
4. | Cooling time can be shortened, therefore productivity increase. |
5. | Improved mechanical strength of the parts therefore higher product quality |
6. | Smoother and better surface appearance therefore better looking products |
7. | Increase regrinds percentage, therefore lower production cost. |
Self-Cleaning
RUMASS Static mixers are designed with no “dead zones”, concerns of how to clean static mixer outside the nozzle is not necessary; on the contrary, static mixer can provide a faster color change in the nozzle.
Color change:Only 3-5 shots is needed for color changing (Polymer PC)
Conclusion
RUMASS Static mixers are more and more frequently used in plastic processing. Homogenized melt for color and temperature is a key factor of producing flawless parts.
For plastic injection molding processing, RUMASS static mixers can improve with a tuned up nozzle performance through a high effective mixing with a low pressure drop. Manufactured by hardened special tool steel gives a long life time and can be applied for glass fibers.
- Lowering Cycle Times
- Improvement of Surface Quality & Value
- Resolving Color Variation