2014.04.16
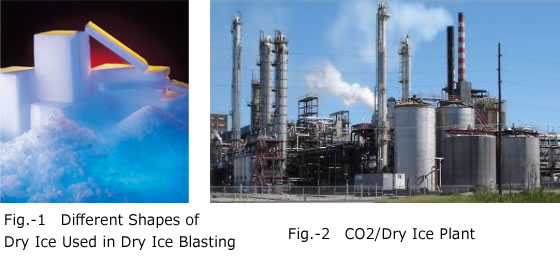
Achieve Green Molding (8)
Continued from my previous article.
◆Solution to Problems with Gas (2)
Last time, Iijima of Matsui Mfg. Co., Ltd. presented various problems caused by generation of gas and the products for solving gas problems, which can be provided by Matsui Mfg. Co., Ltd., under the title of “Solution to Problems with Gas.”
Maintenance work of gas-adhered metal molds is very troublesome. This time, Mr. Inagaki, General Manager, Showa Denko Gas Products Co., Ltd., Industrial Materials Dept., a member of the Association of Green Molding Solutions, presents a system powerfully supporting maintenance of metal molds, possessed by the same company, as a solution capable of greatly reducing this maintenance work in a safe manner.
“Maintenance of Metal Molds by Dry Ice Blasting”
Dry ice blasting accelerates and clashes dry ice against an object at supersonic speed by compressed air, thereby making a small blast on the object surface to remove an unnecessary material.
(See Fig. 8. Principle of Dry Ice Blast Cleaning)
Sand blasting and soda blasting may look alike, but these methods use abrasive media which grind (damage) the surface, whereas dry ice blasting uses a non-abrasive medium so as not to damage the object. (See Table 1. Comparison with Other Cleaning Methods)
This time, I will present dry ice blasting. Now, let us take a look from a different perspective.
1. Relations between Dry Ice and Blasting
Dry ice blasting has been briefly introduced above. Before getting to the point, I will explain first, “Dry Ice and Its Importance.”
You often see block-shaped dry ice used for cooling ice cream, etc. I think you already know that it is made from carbon dioxide. To begin with, I would like to explain that the quality of dry ice is also an essential requirement for blast cleaning.
Currently, dry ice blasting mainly uses 3-mm pellet type dry ice. Naturally, required as a blasting medium is high-quality exclusive dry ice with sufficient hardness. Unfortunately, however, many dry ice manufacturers actually divert pellet dry ice which is originally intended for cooling.
Dry ice blasting technology feature the following:
1. “Impact” – Changes clash energy depending on the speed from a nozzle and hardness of dry ice.
2. “Cooling” – Cools a base material and an object by a drastic temperature difference to promote removal action.
3. “Expansion” – Dry ice in a tiny gap of the object expands abruptly to form a state like a small blast. These three factors decide a cleaning force.
In short, the cleaning force depends greatly on the quality of dry ice.
Dry ice blast cleaning maximizes its capability by using high-density dry ice.
By now, you have understood how important dry ice is.
In the following, I will get to the point.
2. Principle of Dry Ice Blasting
Dry ice is accelerated through a high-speed nozzle and clashes against the cleaning surface. When this is done, kinetic energy and thermal impact of dry ice are combined to destroy coupling of contaminants to the surface.
The contaminants are easily removed from the surface. Dry ice particles make a small blast and sublimate by a clash impact, causing no secondary waste as well as downstream contamination. This is the cleaning principle of dry ice blasting. (Upper illustration in Fig. 8. Cleaning Principle)
This blasting process uses two types of dry ice media; 3-mm pellets (Cold Jet Aero series illustrated on the lower left in Fig. 8. Cleaning Principle) are suitable for removing persistent contamination, and shaved block dry ice (Cold Jet Micro Clean series illustrated on the lower right in Fig. 8. Cleaning Principle) is suitable for cleaning delicate materials, complicated geometries or small openings.
(Dry ice block shaving technology and feeder technology are patented by Cold Jet.)
3. Now, let us see the differences from other cleaning methods.
(Table 1. Comparison with Other Cleaning Methods)
As you see, the best features of dry ice blasting are;
1. “Generation of no secondary waste”
2. “Use of non-abrasive cleaning medium”
Owing to these merits, dry ice blasting, a non-conductive dry cleaning process, allows you to clean the equipment while it is still hot, saving a time and labor to cool and warm up the equipment again according to a production plan.
◆ Dry ice blasting saves a time and labor to disassemble and move the equipment, reducing production cost (shorter shutdown time). Dry ice is non-abrasive and does not damage the surface of the molding equipment or the equipment itself.
Since you do not need to disassemble the equipment or move the hot equipment, the risks involving the equipment and personnel are reduced, which may result before and after the cleaning process.
◆ The percent defective can be lowered by periodic and perfect cleaning which does not blunt or abrade the metal molds.
The operator’s safety is secured by shortening an exposure time to chemicals and hot molds.
Since the mold can be cleaned while being set in the press, including a vent and an injector pin, overall disassembly intervals are extended, contributing to a longer mold life.
◆ Dry ice blasting saves a time and labor to move and disassemble the equipment, reducing the risks of damage and misalignment associated with reassembly.
4. Now, let us look at an actual cleaning example.
As shown in Fig. 9, you can see that the mold is being cleaned without being disassembled/removed. Also, the mold is not being particularly cooled. It is possible to reduce product cost by greatly shortening a cleaning time.
Fig. 11 and Fig. 12 show the state before and after cleaning. You can see that the small vent in the center has been neatly cleaned.
5.Conclusion
Due to the current economic conditions, it is requested to enhance productivity and reduce cost without lowering product quality, and emphasize plant management in order to reduce waste.
If an increasing number of molded product producers are committed to efficient manufacture and comprehensive preventive maintenance, they will understand the advantage of dry ice blast cleaning as an effective and environmentally friendly process, that is, the possibility of multitasking while reducing an effect on production with a shorter time and less resource.
- Shortening Set Up Times
- Cancelling Problems with Gas