2014.03.13
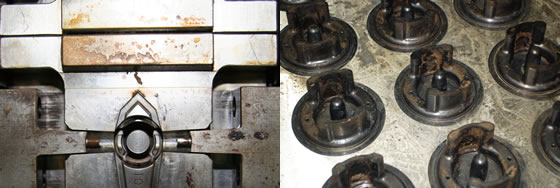
Achieve Green Molding (7)
Continued from my previous article.
◆ Solutions for Cancelling Problems with Gas (1)
Matsui proposes “factor4” as the primary target in molding factories. As a partner for resource conservation, our goal is to help customers achieve 4-times resource productivity by eliminating waste and increasing output.
In the previous issue (sequel to the “Solving Water Quality Issues”), I talked about the problems of the open type cooling tower and closed type cooling tower. I also introduced the Dry-cooler ‘ecobrid’ a next generation cooling tower that overcomes those problems.
Today, I will talk about solutions for eliminating mold problems and defects caused by resin gases released during the molding process.
It might be difficult to imagine gas emissions from plastic resin, for people who don’t work in a molding factory. But actually, in the process of molding plastic, we see gas emissions occurring in multiple places; during the drying of resin, while melting in the molding machine cylinder and as the molten plastic is injected into the mold. Not only that, gas can also occur from the molded part after production.
Result of gas adhering to the mold (Precision molding die / Rubber molding die)
If gas is generated along the mold surface, it can cause defects in the surface quality of the molded product (Transfer failure, Burns, Silver Streaks, Black Streaks, Discoloration, Cloudiness, etc.). If a vent in the mold gets clogged by Gas, it can lead to other defects like a misshaped product or dimensional variation. A clogged vent may also cause insufficient filling of the mold, sinks, voids, bulges, release resistance, and corrosion. In addition, vaporized gasses can solidify and adhere to the mold. The mold may be permanently damaged if processing continues in this state.
These gases consist mainly of additives blended into the resin. Stabilizers, antioxidants, lubricants, flame retardants, plasticizers, and antistatic agents, etc. It is these components that partially vaporize as the resin is heated and melted. Later these vapors condense and solidify onto nearby surfaces. A variety of countermeasures must be considered because the types and locations of these problems are numerous.
Since it is not possible to change the composition of the resin used, and in general, the shape of the molded article (Changing the shape of the end, the wall thickness, the gate position), review of the molding conditions (Injection speed, pressure, temperature, etc.), is required to find methods to suppress the generation of the gas.
Efforts to reduce the occurrence of gas include, vacuum drying, heat transfer drying, starvation supply, and even changing injection screw design. Modifying the screw’s mixing section or compression ratio can sometimes be helpful in reducing the generation of gas. Other steps might include air venting the runner gate, or adding additional mold vents.
Matsui manufactures and sells molding machine peripheral equipment designed to alleviate gas issues. This lineup consists of the DPD3.1 Thermal Conduction Vacuum Dryer, DPD3.1 + Nitrogen, PMD Thermal Conduction Dryer + Nitrogen Generator,
and the GTE-1 ‘Gas Trainer’ which extracts gases generated in the molding machine cylinder.
However, as I have said previously the causes of gas generation and the places where it can occur vary greatly. Time and effort may be required to find counter measures that are effective in each case. It may not be possible to completely vanquish the negative effects caused by the presence of gas. Even if the generation of gas is suppressed, it doesn’t mean all gases will be eliminated. Even degassing vents placed in a mold, will eventually become obstructed by deposits.
When we think about the situations mentioned above, it is clear that resin gassing is an important consideration when making decisions about a molding process. And that regular mold maintenance is essential for maintaining accuracy and quality of the molded part.
Not to be overlooked is the reality that mold maintenance is often a difficult, labor intensive task. It requires shutting down the machine, waiting for the mold to cool, pulling the tool out of the machine and cleaning it for several hours with a brush and solvent on a work bench. Care must be taken by the technician not to damage the mold in the process. The chemicals used are strong so worker safety must be insured. Once completed the tool must be reinstalled in the machine and allowed to reheat before production can be restarted. While necessary, this task costs time and money.
In fact, it is not a panacea, but we can recommend solutions which will greatly reduce the time and effort normally needed for mold maintenance.
To be continued…
- Cancelling Problems with Gas