2014.04.16
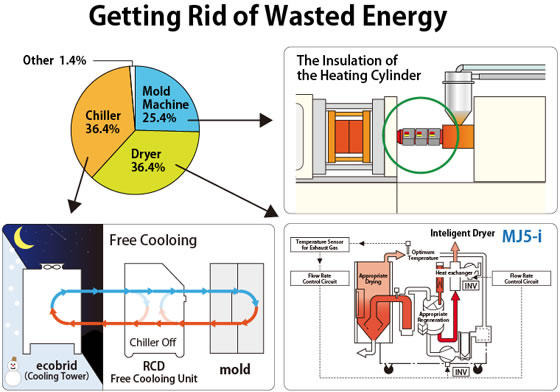
“Doubling Wealth & Halving Resource Use” (7) --- Getting Rid of Wasted Energy (1)
7. Getting Rid of Wasted Energy (1)
In my previous article I introduced “Heat & Cool Molding” for lowering cycle times. In this article I will describe solutions to get rid of wasted energy.
First, let me show you one example of energy consumption in an injection molding line.
Generally speaking, the keys to saving energy in the injection molding cell are found at the cell’s;
1)Injection molding machine
2)Dryer
3)Chiller
Our association offers the several solutions to save energy in these machines as shown in the figure below. For example, regarding the injection molding machine, the insulation of the heating cylinder is very effective, in addition to using the all-electric injection machine. We offer several kinds of insulator for the cylinder.
Hereafter I would like to focus on saving energy with the other 2 machines mentioned, the dryer and chiller. Let me take the dryer first.
Why does the Dryer consume so much of the total energy in the molding cell? One of the biggest reasons is poor energy efficiency. Typically dryers run at far more capacity than the molding cell’s production demands. This poor efficiency can be traced back to the methods used for selecting a dryer.
An example of choosing the appropriate dryer would be like that below.
In a particular molding line, under the best possible conditions, a maximum of 9kg of resin per hour is consumed.
↓
Leaving some leeway, a dryer that can dry 10kg/hr will be sought out.
↓
Dryer manufacturers like Matsui, will suggest a dryer that has capacity for at least 12kg/hr, for added safety.
↓
In some cases a dryer with a 12-kg/hr capacity may not be available, so a dryer with 15-kg/hr capacity may be suggested to the user.
As a result, the following situation occurs.
・A line that requires drying capacity of 9kg/h is being fixed with a dryer that dries 15kg/hr.
・Furthermore, the requirement of 9kg/hr has been derived from under best possible conditions that are usually not the case.
・In addition, molding is not carried out at full force all the time. It may be halted for exchanging of mold or maintenance.
・A dryer that dries 15kg/hr is running at full force under such circumstances.
That being said, under normal conditions, about half of the dryer’s energy consumed is wasted. Even worse, most of this wasted energy is exhausted to plant as heat. This waste heat forces the factories climate control system to work harder to maintain the desired plant temperatures. Thus even more energy is wasted.
How is it possible to prevent such waste? The main reason behind these inefficiencies is the resin dryer’s inability to adapt to changing demands. Dryers are usually selected to handle the biggest and toughest molding jobs. However these jobs are not run all the time. Therefore dryers which can only run at full capacity will waste a great deal of energy much of the time. In order to eliminate this waste, it is essential for drying power to be adjusted according to varying resin volumes. So, how can we adjust drying power without affecting drying quality?
To be continued.
- Getting Rid of Wasted Energy