2013.12.17
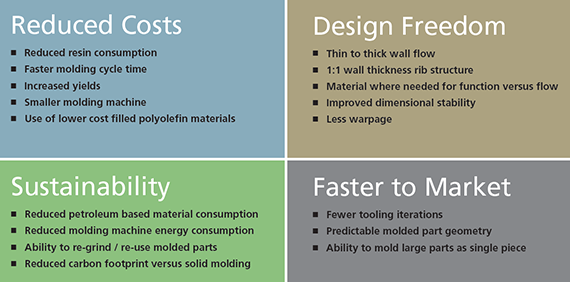
MuCell® Microcellular Foaming Technology for the Injection Molding Industry: The most significant plastics processing innovation in the last 20 years
MuCell® Microcellular Foaming Technology for the Injection Molding Industry: The most significant plastics processing innovation in the last 20 years
The MuCell® microcellular foam injection molding process for thermoplastics materials provides unique design flexibility and cost savings opportunities not found in conventional injection molding. The MuCell® process allows for plastic part design with material wall thickness optimized for functionality and not for the injection molding process. The combination of density reduction and design for functionality often results in material and weight savings of more than 20%.
By replacing the pack & hold phase with cell growth, lower stress parts are produced which have enhanced dimensional stability and substantially reduce warpage. Cell growth also results in the elimination of sink marks. Unlike chemical foaming agents, the physical MuCell® process has no temperature limitation and does not leave any chemical residue in the polymer; making consumer products perfectly suitable for recycling within the original polymer classification and allowing re-grind material to reenter the process flow.
The numerous cost and processing advantages have led to rapid global deployment of the MuCell® process primarily in automotive, consumer electronics, medical device, packaging and consumer goods applications.
The MuCell® Application Advantage: The freedom to design for functionality and not for plastic process limitations
By replacing the tradition pack & hold phase of the solid molding process with cell growth, the MuCell® process allows for uniform and locally applied pack pressure through cell growth. This allows part design to be optimized with material thickness in those areas that require strength and reduced wall thickness in areas that are not structural. Gate locations are then placed in the thin cross sections for optimized filling patterns while allowing the cell growth to provide packing in the thicker cross sections at the end of fill.
Using the same principle, nominal wall thickness can be reduced while using thicker ribs to meet structural requirements. The cell expansion will eliminate sink marks and the cell structure will prevent the formation of vacuum (shrink) voids. Rib to wall thickness ratios of 1:1 can be used with the MuCell® process.
About Trexel
MuCell® Microcellular foaming technology was originally conceptualized and invented at the Massachusetts Institute of Technology (MIT) and in 1995 Trexel was granted an exclusive worldwide license for the further development and commercialization of the technology. Today, Trexel is the exclusive provider of the MuCell® microcellular foam technology and maintains an extensive global patent portfolio. Trexel provides world-class engineering support, training and other design and processing services, as well as the equipment and components integral to the MuCell® process.
From the global headquarters in Boston, Massachusetts, Trexel operates a state of the art plastics processing development laboratory, supporting plastics processors with the definition and implementation of leading and differentiating plastic molding technologies.
In support of a global client base, Trexel operates subsidiaries in Europe, Japan and Southeast Asia with competent plastics processing engineering capabilities. Trexel’s worldwide subsidiaries are augmented by a network of competent independent representatives and distributors.
- Getting Rid of Material Waste
- Lowering Cycle Times
- Lightening Part Weights
- Higher Dimensional Precision