2013.10.15
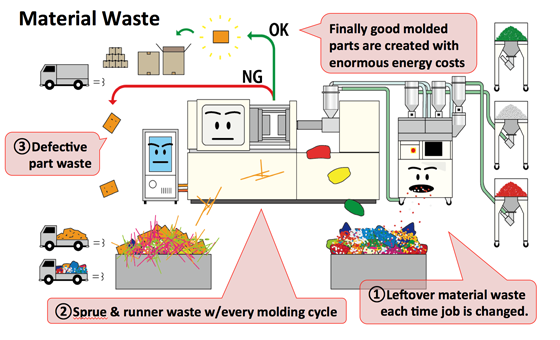
Achieve Green Molding (2) --- The Solution of the eliminating Material Waste
◆ The Solution of the eliminating Material Waste
We, Matsui, propose “factor4” as a primary target in molding factories as a partner for resource-saving. Our goal is to help customers achieve 4-times resource productivity by eliminating “Energy waste”, “Resin waste” and “Water waste”.
We introduced general information about the iplas series produced from the development efforts to achieve the ‘factor4’ on my previous issue. We will talk focusing on ‘Resin waste’ in molding factories within this issue.
As you all know, because plastic molding products are wide varieties, and life cycle is getting very short. We need to change resin frequently to meet the demand on small amount of multi-items production in the plastic molding business recently.
As every final product requires various material and color with each molding, different combination of material and color is required for each product, and then left over material needs to be discarded for the next product.
Also a sprue runner could be bigger than the molded article depending on the product a lot of cases, I would think these are discarded without being recycled.
If any defectives are found, the final products produced at the cost of various waste will be discarded also. It is hard to imagine how much of resin is wasted before the final product produced.
We, Matsui, looked into eliminating waste of resin as much as possible.
There are three important points when we have reviewed the material blending and supply process as per above chart.
First, reduce the amount of mixed materials staying in apparatus.
Second, Recycle of sprue runner.
And third, Stabilize the forming quality and reducing the defective.
First, we focused on the ‘waste of resin’ in the process of material blend and supply, and began development of the equipment.
We have achieved 99% reduction of wasting of left over resin by optimum mixture, the control of material supply of the minimum requirement, and integration with production planning registration function.
In addition, besides eliminating the waste of resin footprint of equipment is also down by 47% compared to the conventional model due to the compact design.
And it prevents contamination by ability to clean easily, and also it helps to reduce of the material changing time.
The JCW2-i, which was completed by development aiming at ‘factor4’, became innovative system that adjusts the amount of material supply autonomously in accordance with the usage of resin by the molding machine.
We named this feature ‘iplas’, and that led to the development of “i“ series, such as Temperature Controller, Dryer and Granulator.
(To be contined.)
- Getting Rid of Material Waste