2014.12.01
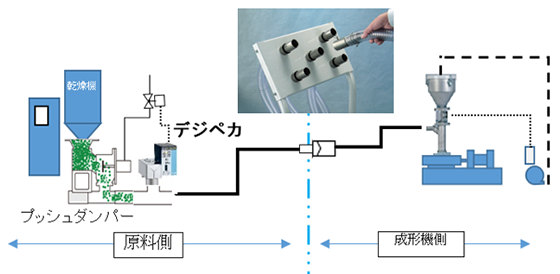
「デジペカ」システムによる原料供給システムの段取り時間の短縮
前回の記事より続く。
「デジペカ」システムによる原料供給システムの段取り時間の短縮
前回は1by1の乾燥システムを例に段取り時間について説明しましたが、このシステムには未だ課題が隠れています。そして、成形機が複数台になるとその隠れていたものが表面化して生産効率を妨げます。このようなケースに効果があるのが原料供給システムです。原料供給システムは費用が高い事や設備後の自由度が低い事を理由に導入を躊躇している方もいると思います。
今回は設備後の変更も簡単にできて安価な費用で設備できる「デジペカシステム」の説明をしたいと思います。
では、4台の成形機を例にデジペカシステムを説明していきます。前回記事で引用した図6のフローを使って成形機4台のモデルを図7に示しました。図7は単純に1by1のシステムを4式並べたものです。図の中に4つの課題を記しました。
図7
図7の課題を内段取りと外段取りのどちらに該当するかを表2にまとめました。
表2 課題の整理
課題 | 内段取り | 外段取り |
①交換する乾燥機と成形機ホッパーのレベル計仕様が違うとその対応に時間が掛かる。 | ○ | |
②原料を替える度に原料ホース、空気用のホース、信号線の差し替えに時間を費やす。 | ○ | |
③乾燥機を移動、入れ換える時間がムダ | ○ | |
④乾燥機の全体の利用状況を管理できない。 | ○ |
前回の繰返しになりますが内段取りとは生産を止める事ですから、生産量が減少して直接コストを上げる要因になります。一方外段取りは直接的にコストを押上げる事はありませんが管理費に影響し最終的には製品コストへ配賦される事になります。それでは、図7にある課題の原因について図8で説明します。
図8
図7の1システムをクローズアップしたのが図8です。図8を見ていただくと分かるように成形機側と原料側に吸引用ホース、計装電気配線、原料用ホースが跨って繋がっています。外段取りで準備した乾燥機と入れ替える場合はこの繋がっているものを繋ぎ替える必要があります。その結果表2の内段取りである①、②の課題が発生する事になります。前回の記事では原料抜き作業を中心に改善の話をしましたが、未だ乾燥機の入替え作業に課題があったという訳です。ではデジペカシステムではどのようになるのでしょうか。図9で説明したいと思います。
図9
図9を見ていただくと計装電気配線と吸引用ホースが成形機側と原料側に跨っていないことが分かると思います。これで図8の①と②の課題を解決できます。そして、この事は異なるメーカーの乾燥機や倉庫に眠っていた遊休機でもシステムで使えるという意味で価値があります。ではこのような事を可能にするデジペカとはどんな仕組みなのか気になるところです。
デジペカにはスイッチ部と制御部があります。
図10
スイッチ部は吸引ホースに吸引圧が作用する状態で取り付けます。原料輸送の吸引圧でスイッチが入り制御部に信号が入り制御部がプッシュダンパー等を制御する仕組みです。流れをまとめて説明すると
“成形機上のレベル計ON(電気信号)→ブロワー吸引(吸引圧が電気信号に代わる)→デジペカSWがON(これ以降電気信号に戻る)→デジペカ制御回路が起動→プッシュダンパー(開)→デジペカ制御(タイマー又はカウンターアップ)→プッシュダンパー(閉:ホースは中の残留原料が送られ空になる)→ブロワー停止→デジペカスイッチOFF”といった感じになります。(余談ですがデジペカのフルネームは“デジタルペッカー”と言います。これはデジペカのスイッチ部が、啄木鳥が嘴で樹木を叩く様子から連想したこと、制御盤にマイコンを搭載している事に由来しています。)
次にデジペカを使ったら前述の図7のシステムはどうなるのでしょう。それを図11にフロー図化して表してみました。
図11
図7と図11を比較して成形機と乾燥機の台数は変わりませんが、図11では乾燥機8台で原料の繋ぎ口が12方向あります。(もちろんこれは2方向で使う乾燥機には能力を2台分有している事が必要です。)そして、原料の切替えを下の写真のような簡単なコネクションユニットに集中化でき、乾燥機を移動させる必要がなくなります。この事から表2の③、④の課題を解決できます。改めて表2の課題を登場させて表3として確認します。
表3フローの比較
課題 | 図7 | 図8 |
①交換する乾燥機と成形機ホッパーのレベル計仕様が違うとその対応に時間が掛かる。 | 課題あり | 解決した |
②原料を替える度に原料ホース、空気用のホース、信号線の差し替えに時間を費やす。 | 課題あり | 解決した |
③乾燥機を移動、入れ換える時間がムダ | 課題あり | 解決した |
④乾燥機の全体の利用状況を管理できない。 | 課題あり | 解決した |
最後に効果のチェックをしたいと思います。
表3の①、②、③の課題で平均30分の改善ができたとすると生産時間が年間1000時間拡大します。(原料替え回数500回×0.5時間×成形機4台=1000時間)
又、表3の④の課題は、解決しても外段取り作業ですから直接コストとして評価されませんが、どの成形機と乾燥機が繋がっているのか、どの乾燥機が空いているのかが直ぐ分かる事で外段取りの合理化ができます。
以上
- 段取り時間の短縮