2013.10.15
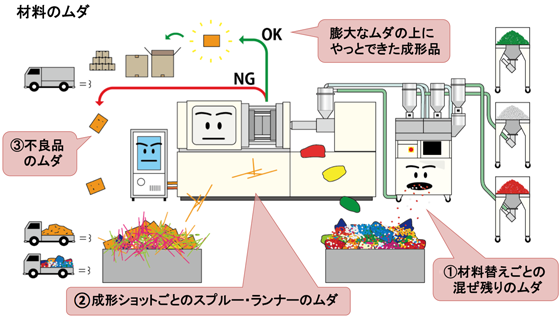
グリーン・モールディングの実現に向けて (2)
◆ 樹脂のムダを無くすソリューション
私たち松井製作所は、成形工場の資源節約パートナーとして成形工場の「factor4」の実現を提言しております。「水のムダ」、「樹脂のムダ」、「エネルギーのムダ」を無くし、成形工場の資源生産性を4倍にする事を目指しております。
前回は、この 「factor4」 実現に向けた取り組みの一つ、製品開発から生まれた iplas シリーズ全般についてご紹介させていただきました。今回は、成形工場における「樹脂のムダ」に焦点を当てて、お話させていただきます。
皆様ご存知の通り、近年では、樹脂成形品の種類は多岐に渡り、製品のライフサイクルも短いため、多品種&少量生産が、ますます求められてきています。こうした要求に応えるためには、短い期間で、次々と材料を替えていかなければなりません。
成形品によって使用する樹脂や色が変わるので、その都度配合が必要となり、前の成形で使用した混合済みの材料が、後の成形に混ざらない様、装置内に残った材料は全て廃棄されてしまいます。
また、成形品によってはスプルー・ランナーの方が大きい場合も多々ありますが、これらもリサイクルされる事なく、その殆どが廃棄されているのではないでしょうか。
多くのムダを重ねて出来上がった成形品も、不良が出れば、ここでもまた廃棄されてしまいます。製品ができるまでに、一体どれだけの樹脂をムダにしているのでしょう。
松井製作所では、この樹脂のムダをできるだけ減らす方法を考えました。先程の成形行程を見直してみますと、装置内に滞留する配合材の量を減らす事、スプルー・ランナーのリサイクル、そして成形品質を安定させ不良を減らす事、この3つがポイントとして上げられます。
そこで私たちは、まず初めに、成形行程の入り口に位置する原料配合/供給の工程に着目し、 装置の開発にとりかかりました。
混ぜ残りが発生する工程を見直し、そして、省資源を実現するための様々な工夫と取り組みから、最適な配合、及び必要最小限の材料供給のコントロール、生産計画登録機能との連動により、これまで装置内に残ってしまっていた配合材を、最大で 99% まで削減できる様になりました。
更に、樹脂のムダを無くすだけでなく、コンパクト設計により寸法そのものも小さく、設置面積では従来機と比べ 47% もダウン、また、高い清掃性によるコンタミの防止、材料換えの時間短縮にも効果を発揮します。
そして何より、factor4 実現に向けて開発された JCW2-i は、装置自体が成形機の樹脂の使用量に合わせて自律的に材料供給量を調整する、セルフコントロール機能を搭載した画期的なシステムとなりました。
この自律的に考える機能を iplas と命名し、以降、順次世に送り出されています、温調機、乾燥機、粉砕機の iシリーズの開発へとつながりました。
- 樹脂のムダをなくす