2013.09.27
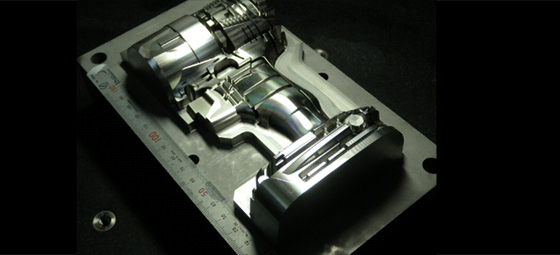
金属光造形複合加工の劇的進化と運用方法の注意点、高度化 (1)
1. はじめに
株式会社OPMラボラトリーは、パナソニック株式会社様から正式ライセンスを受けて金属光造形複合加工用制御ソフトウエアの基本アルゴリズムからソリューションシステムを創業以来10年継続開発し、同時に工法原理の高度化開発を今もなお継続的に行っている。
金属光造形複合加工装置専用装置の松浦機械製の「LUMEX」には、なくてはならない専用レーザ及びCAMシステムとしてご提供をしている。
もう一つの顔をとして、世界最大数の装置を保有しマスプロダクションとして利用しているパワーユーザでもある。ちなみに金属光造形複合加工装置の製作及び市場参入は、パナソニック株式会社様から開発権利を取得し装置開発をすることが可能である、日本製造力強化の観点では、複数の装置メーカが参画し、競争しながら装置をさらに高度化させ、競争しながら普及することが望ましい姿であると考えている。
本題に入る前ですが、安易な考えで創業したものの、10年前時点の本工法は、装置、原理自体が未成熟で課題が山積し、毎日が失敗、苦労の連続、本当に実戦で使える日が来るのだろうかと眠れない日々を過ごし、いつ倒産してもおかしくないという状況であったことを記憶の中に今も深く鮮明に残っている。今では、3Dプリンターというキーワードで、新聞、テレビ等のメディアで目にしない日がないぐらいに市場が沸騰しているという状態で、弊社にも通年の4、5倍の御引き合いが集中しており、時代の変革期を目の当たりにしている。
本稿では、私が毎日悩み苦労をしてきたユーザの立場、視点にて、金属光造形技術を解りやすくレビューし、今後この工法を自社の金型技術として取り入れようとしている方々の参考になればと寄稿をさせて頂く。紙面ではありますが、ご協力を頂いた関係各位に心から感謝を申し上げる。
2. 金属光造形を高精度部品に適用する為、切削複合方式でなければならない理由
金属光造形は、平均粒径20~30μの金属粉末をレーザで溶融しながら積層していく技術であることは、多くの方が既にお知りであると考える。(基本的な工法の説明は省略をする。)実際には、約1400~1500℃のレーザ熱源を、走査線状に金属粉末へ照射し溶融させ、固化する。この原理は、レーザ溶接と同様であり、溶接物同様に造形物内には、残留応力が発生する、同時にプレートと造形物の境界面に応力が生じプレートに反りが発生する。間違った設計をすることにより、プレートと造形部に亀裂が生じ、精度は愚か
部品として全く利用できない「ただの鉄くず」になってしまう(Photo1)。
この応力を適切に弛緩させ、反り発生量を予め予測し、事前に適切な対策が取れるかが、高精度部品へ適用するための重要なポイントである。
実際に産官学で取り組んだ戦略基盤技術強化事業の中でも大変重要なテーマとして位置付け、評価試験を行い、その結果の一例をGraph1に示す。グラフに示すように、プレート厚みに対して、一定高さを超えると反り量が増加しないことが解っている。(ただし、造形材料、造形面積とプレート厚/材質にも依存する)。弊社では、造形体積と投影面積による反り量の予測曲線を用い、個々要求精度に応じた適切なプレート材質、厚み設定をした上で、必ず造形物の一定高さ以上に2次加工用切削基準面を設けるようにしている。
±1/100以上の高精度な加工品を、金属光造形を用いて製作する為には、必須事項である。
レーザのみの金属光造形方式は、装置へベースプレートセット後に平行度、位置決めを機械上で測定する機能もなく、造形プレート端面から、或いは穴加工のセンターから中心を割り出すことは、セット段階で正しく位置決めされていない理由もあり、プレートは単なる台座としてしか使えない。
又、ガルバノシステムが自動補正されているとは言え、熱膨張、収縮の繰り返しが長時間発生している為、プレート上へ配置されるCADデータが、カタログ値通りに位置決めが保証される訳でもない。加えて前述の反り問題がプレート上に発生している為、造形完了後に、ワークテーブルから外した瞬間に、プレートが反り返る、その結果、造形物に2次加工を行う際、プレート端面もしくは穴からでは測定できず、どうしようもない事態に陥る。このことは、金属光造形を利用しているユーザが一番注意している点で、装置メーカは、この問題に対し、対策を講ずる為の研究、開発作業は皆無に等しく、弊社は、この課題は量産適用で一番困ることであり、重要視し研究開発継続及び対策検討に余念がない。
このようなことから、レーザのみの金属光造形方式は、レーザで溶融/固化した造形物を、別段取りにて2次加工で行ったとしても、±1/100以上の寸法精度への適用は至難の業とユーザの立場から断言できる。このレーザのみの方式の装置利用の海外ユーザへの見学、意見交換を数多く行ってきた経験からも
精度の必要な部品、金型へ適用する目的で導入しているのではなく、人口歯根、人工骨等の医療系分野或いはデザイン分野で、精度を不要とする事業分野への事業目的であり、機械精度の求められる分野への事業目的は皆無である。(但し、金属光造形品を2次加工プロセス(一般加工機)で加工可能な範囲の形状である円筒、角柱、円錐、角錐、或いはその集合体の部品などの単純な形状への適用は一部であるが実施されている。)
日本は10数年前に一度、レーザのみの金属光造形の導入ブームが起こり、ご導入をされた会社も数社あり、この反り対する問題意識は高い、その結果、日本ではレーザのみの金属光造形装置を精度部品に適用する為に導入しようという企業はほとんどない、しかし金属光造形に関する予備知識の少ない中国、台湾、東南アジアなどにある企業で、金属光造形装置を導入しようという会社の中には、このことを認識していない企業も多く、非常に危険であると考える。
この背景には、欧米の装置メーカが3Dプリンター志向のものづくりを、金属光造形という分野へも
パーソナルユースで利用が進む樹脂版の3Dプリンターとあまり変わりのないプロモーションの方法を取っているためであり、形状確認程度の試作品には使えても、精度が必要なマスプロダクションの生産プロセスへ、適用させようとしていることには困難がある。
大事なポイントとして
・金属光造形装置と前後工程の親和性考慮不足(加工基準、測定基準)
・装置自体の機能不足(測定、数値フィードバック)
上記の2点を見落としており、この視点に本腰を入れ改善を行う必要があると考える。
この重要な事実を見落とし、万が一精度が必要な金型、部品の事業をする為に、ユーザが導入した場合、稼働率は愚か、適応に支障が来たし、装置に埃を被ることになり大変注意をしないといけない点であることを強くアドバイスしておきたく考える。日本が産官学を上げて開発を推進してきた金属光造形複合加工法は、このレーザのみの金属光造形が、高精度金型、部品に適応できない為、どのように解決をするかという視点で、パナソニックの基本特許をベースに、平成15年~平成17年度の戦略的基盤技術力強化事業(金型分野)で基本工法開発を行い、特に平成18年から19年度の地域新生コンソーシアム事業で本格的に市場競争できる実用開発が達成できたと考える、この時のメンバーは「パナソニック、OPMラボラトリー、九州工業大学、金沢大学、宮丸精密金型、ヤマナカゴーキン」という実務レベル企業とこの技術の知見を持つ大学研究室で構成され、約5年間を掛けて課題解決を行ってきた。
この複合方式は、装置内にNC制御/加工スピンドルを実装しているが決して造形物を全て切削で仕上げるということだけではなく、ユーザは、2通りの選択視があり、要望、用途に合わせて最適な方法を使い分けることが可能であると考えるべきであり
① 造形物に2次加工をする為の加工用基準面だけを作成する方法(Photo2)(単純な形状で、装置内で全切削するより、2次加工にて仕上げた方が有効な場合)
② 造形物の全ての面を切削仕上げで行う方法(Photo3)
(リブ等が多く、電極を多数作成しなければならない形状などに有効)
弊社も同様に最適な選択をしながら使分けて生産を行っている。
- サイクルタイムの短縮
- 寸法精度の向上
- グリーンモールディング全般