2014.10.09
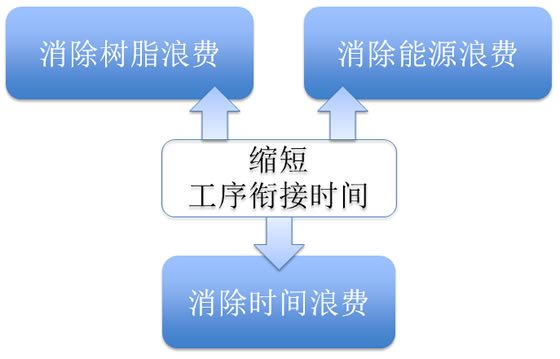
更换材料时工序衔接时间的缩短
更换材料时工序衔接时间的缩短
●缩短工序衔接时间,能带来什么好处呢?
成型机一年的运转工作时间大约为4000小时(注1)。若能缩短其中的工序衔接时间,相应就能增加实际生产时间,从而提高生产量。大多数装置的电力消耗是和运转时间相关联(注2)。运转时间相同,生产量更多的话,单位能耗(注3)和用电成本就会更小。在图1中表示「内部工序衔接」和「原料」「时间」「电力」的关系。
从图1中我们能看到「缩短工序衔接时间」后,对「原料」「电力」「时间」成本所带来的益处
图1
(注1) | 1年的运转工作时间按此条件(1天=16小时、1月=21日、1年=12月)来计算,应该是4032小时。方便起见,在上述的描述中简化为4000小时。当然,也有很多公司是以8000小时作为基准。 |
(注2) | 大多数情况下装置的消耗电力是和运转工作时间相关联。下面将介绍一些例外情况。以成型机的实验为例,在缩短成型周期后再比较消耗电力和生产量可以发现,生产量提高30%而对应的电力消耗大约仅上升15%。另外,我公司的MJ5-i系列的电力消耗与其说是和运转时间关联,还不如说是和原料的使用量相关联更为合适。在类似上述的情况下,电力消耗就不一定是和运转时间相关联了。 |
(注3) | 「单位能耗」的含义请参考节能中心专业词汇中的详细说明 ⇒ http://www.eccj.or.jp/qanda/term/kana_e.html#08 对成型来说可简单理解为,生产所消耗的电量除以生产数量后得到的数值。 |
工序衔接时间可分为「外部工序衔接」和「内部工序衔接」。至成型机停机为止是「内部工序衔接」,而到下次成型前的准备是「外部工序衔接」。
在年度生产时间的范围内,若将内部工序衔接的比例最小化,就能有效的扩大生产效率。而说到必要的外部工序衔接,原料的预备干燥和模具的预备升温是典型的外部工序衔接的案例。下面,以干燥系统为例来说明工序衔接时间的缩短。
●更换材料时工序衔接时间的缩短。
以标准的干燥系统为例,我们一起来看一下材料更换时所需的工序衔接时间。在图2的案例中记录了发现的问题点,并在图中的()内记录了花费的时间。
图2
成型机年运转时间为4000小时,以平均8小时更换1次材料来计算,一年就需要更换500次材料。图2()中合计的40分钟,削减30分钟的话,500次×30分钟=15000分钟=250小时。如图3所示,若换算成16台成型机的话,所节省的时间就相当于1台成型机的运转时间。
图3
图3中所示是原料的使用量从3kg到5kg/h,小型成型机的案例。
此案例的解决方案是
1. 成型机上储料量的最小化
2.向成型机输送的批次原料量的最小化
3. 配管中没有材料残存
只要做到以上3点,就能实现目的。而为了实现以上3点,就必须用到下面介绍的定量排放装置和仅存储少量材料的APHG。
●定量排放装置
定量排放装置直接安装在干燥机下部。1次排出的原料量,控制在50到150g的范围内。(这个数值是以成型机上的滞留时间以2~6分钟为依据而设定。)
图4
图5
●存储少量原料的小料斗 APHG
APHG被当做成型机上的小料斗来使用。小型APHG的场合,从成型机的入料口到要料料位计的存料量为60到100g。定量排放装置和APHG的组合使用,就能实现原料滞留时间的最小化。一个对小细节问题的考量,就能对工序衔接时间的缩短的实现产生很大的效果。
图6中描述了定量排放装置和APHG对残材排出问题的改善。在生产终止前停止原料的输送,仅以剩余的原料进行最终的成型,这样就不再需要花费时间来排空残材。
图6
●材料更换时缩短工序衔接时间的效果
缩短工序衔接时间,就能增加生产量,获得很大的价值。同时,对原料和电力成本的控制也能带来很大的影响。请详见表1中的总结。
表1 缩短工序衔接时间的效果
未完待续。
- 消除能源浪费
- 消除树脂浪费
- 缩短工序衔接时间